Is your robotic palletizing or depalletizing system reliable and efficient?
Robotics palletizing and depalletizing systems often face challenges that limit their reliability and efficiency. These issues are misaligned or damaged products, different product dimensions, stacking patterns, and missing labels or QR codes that can lead to operational delays and costly errors. Additionally, dependency on human oversight for error defection and readiness checks increases labor costs and slows workflow. Groundlight solution addresses these problems by answering the following questions as shown below and provide real-time monitoring:
Problem: Is your robotic palletizing or depalletizing system reliable and efficient?
Without real-time monitoring and intelligent error detection, palletizing and depalletizing systems often require human intervention, reducing efficiency and increasing labor expenses. Many palletizing and depalletizing systems struggle with these common challenges:
- Misaligned or damaged products leading to unstable stacks.
- Dependency on human oversight for error detection.
- Missing QR codes, labels, or readiness indicators for palletizing.
- Inefficiencies in depalletizing tasks due to misplaced, damaged, or incorrect items.
Current alternatives
While some businesses still rely on traditional methods for palletizing and depalletizing, these approaches come with significant drawbacks. Without advanced vision systems, automation remains rigid, error-prone, and dependent on manual oversight, limiting efficiency and scalability.
- Manual inspections or interventions.
- Cobots without vision systems, relying on fixed programming.
- Static vision systems with limited adaptability to changing workflows.
Groundlight’s solution: Robotic palletizing/depalletizing using computer vision
Groundlight’s Visual Inspection & Anomaly Detection integration with Universal Robots transforms Universal Robots (or any cobot) into smarter systems by adding real-time anomaly detection, adaptability, and precision monitoring to their workflows.
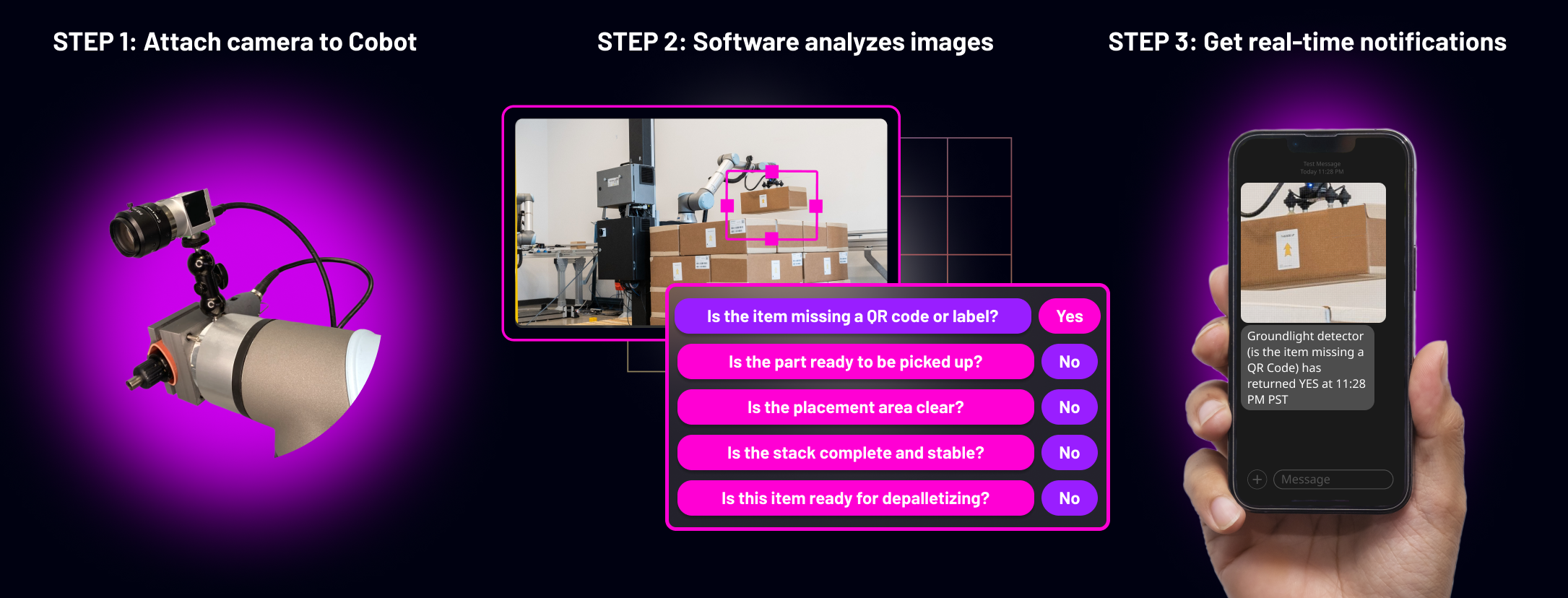
Critical questions answered by Groundlight
- “Is the fixture correct?”
- “Is the part ready to be picked up?”
- “Is the placement area clear?”
- “Is the stack complete and stable?”
- “Is this item ready for depalletizing?”
- “Is the item missing a QR code or label?”
Key features
- Anomaly Detection: Real-time detection of misaligned products, damaged items, missing or QR codes.
- Real-Time Monitoring & Customizable Actions: Proactive alerts for issues, and you can even customize what action the robot should take in response to that issue (ex: robot puts aside the damaged product from the stack).
- Workspace Safety Monitoring: Ensures workspace readiness and fixture accuracy.
- Error Prevention in Depalletizing: Identifies readiness issues, for example a damaged package or missing labels.
- Scalability: Supports high and low volume environments.
Impact
- Proactive Issue Resolution: Identifies and helps resolve anomalies in real-time. Anomalies like misaligned products, incomplete stacks, missing labels or damaged packages.
- Reduced Costs Through Intelligent Monitoring: Minimizes rework, waste, and downtime by detecting and addressing errors in real time such as damaged products or misplaced items before affecting the downstream process.
- Enhanced Safety and Workspace Readiness: Monitors workspace conditions, detecting hazards like obstruction or foreign objects, and ensuring consistent operational safety.
- Scalable and Intelligent Operations: Adapts to high-mix and low-volume environments, learning and improving over time to support evolving workflows and product variations.
How Do I Get Started?
If you are a developer or have developers in-house, here’s how you can build this solution for yourself
Schedule a demoIf you’d like to customize this solution for your business but need assistance to get started, book a call with Groundlight and we’d be happy to help
Schedule a call