The Problem We Are Solving: Detecting Common Defects in Plastic Injection Molded Parts
Does this part have excessive flash?
Is the part fully molded?
Plastic molded parts are components manufactured by injecting molten plastic into a mold, where it cools and solidifies into a specific shape. These parts can range from finished products, like consumer goods and packaging, to critical components used in larger assemblies, such as automotive interiors, electronic casings or medical devices. Maintaining their quality is crucial, as even minor defects can compromise functionality, disrupt assembly processes or lead to costly rework and dissatisfied customers.
Common Defects in Injection Molded Parts
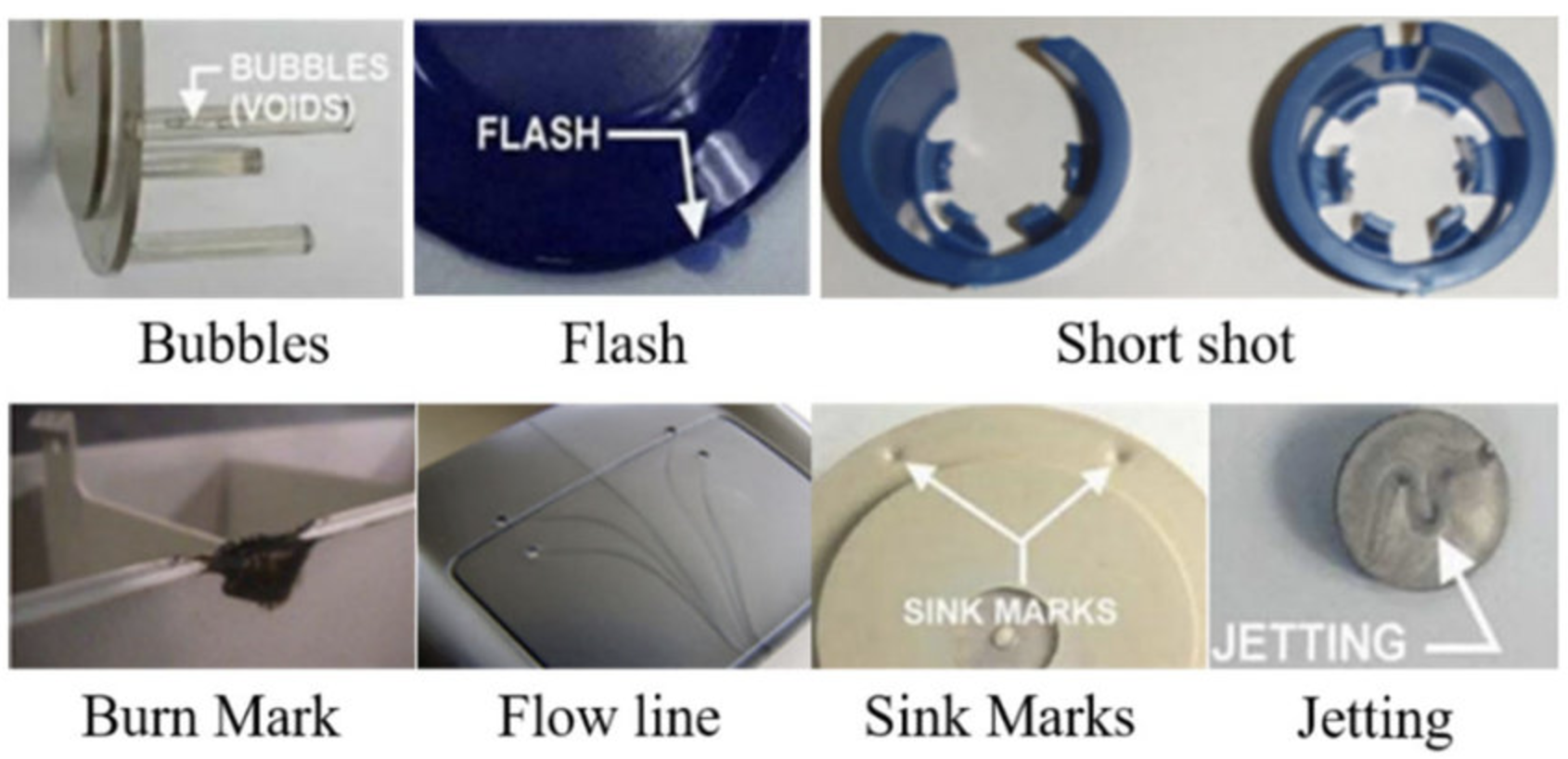
- Flash: Occurs when molten plastic leaks out of the mold cavity at the parting line, creating thin, unwanted layers of material on the edge of the part. These defects not only require additional trimming but can also interfere with the part’s fit or function in an assembly if not addressed.
- Short shots: happen when the mold isn’t completely filled during the injection process, resulting in incomplete or partially formed parts. This defect compromises structural integrity and can render the part unusable, especially in critical applications.
- Missing inserts: Often required for strength or assembly purposes and are molded into the parts during production. Missing inserts can occur due to improper setup or misalignment during molding, leading to parts that fail to meet design requirements or cannot be properly assembled.
- Surface irregularities: flow lines, sink marks, or bubbles can occur during cooling or material flow through the mold. While these may not always impact the functionality of the part, they degrade the appearance and perceived quality.
Current Alternatives to a Real-Time Defect Detection System of Injection Molding
While traditional methods to identify defects in plastic injection molded parts have been used for decades, they often fall short in addressing the speed, consistency, and scalability required in modern manufacturing. Common alternatives include the following:
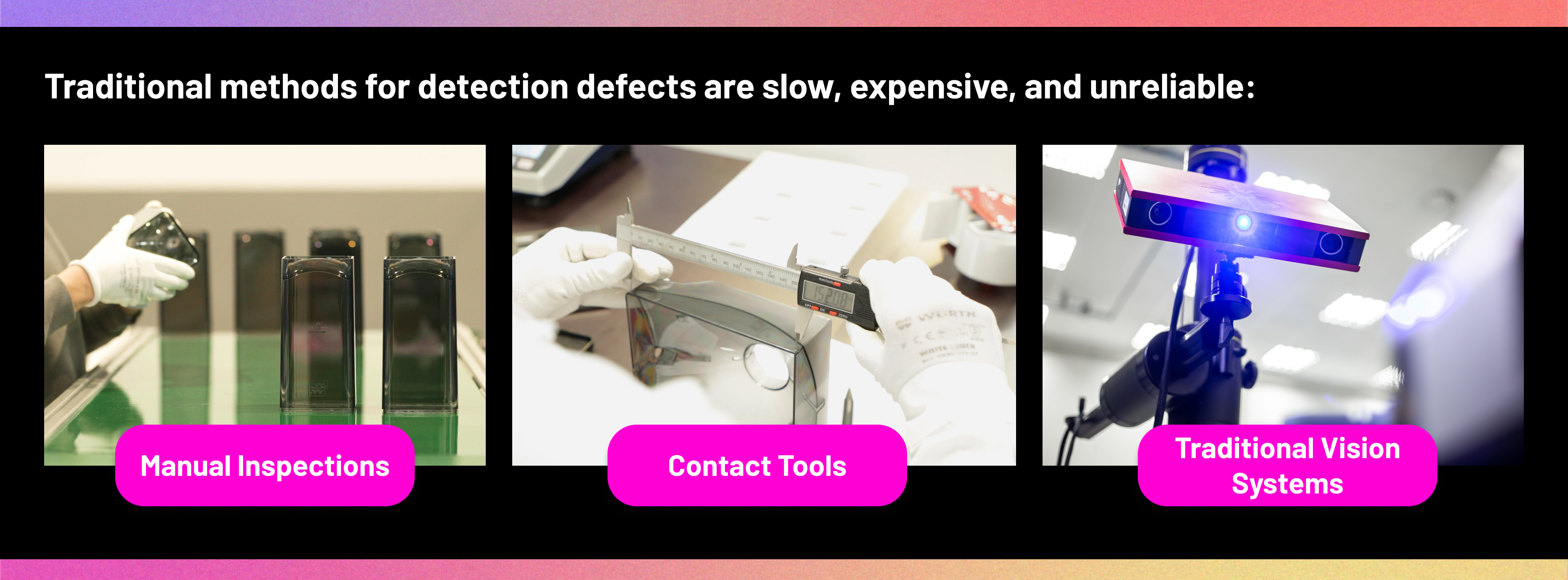
- Manual Inspections: Human inspectors visually examine each part for defects such as flash, short shots, or surface irregularities. This method is prone to inconsistencies due to human error, fatigue, and subjective interpretation. Additionally, manual inspections are time-intensive, especially for high volume production lines. Regulatory requirements, such as mandatory breaks and shift changes, further disrupt continuity, creating inspection gaps during operations.
- Contact Tools: Tools like calipers, gauges, and micrometers are used to measure dimensions and tolerances. While effective for verifying part dimensions, these tools are prone to variability caused by operator technique. Measurement can differ based on where the tool is placed or how much pressure is applied, introducing inconsistencies. Additionally, reading calipers accurately becomes challenging for small tolerances, increasing the likelihood of errors. As these tools rely on manual operation, they are time-intensive and create bottlenecks in high-end production lines.
- Traditional Vision Systems: Automated vision systems used preprogrammed algorithms to detect defects. While they offer faster inspection speed than manual methods, these systems often require extensive customization and calibration for specific defect types or parts. They also struggle with adaptability, making it difficult to scale or apply them to new products or production lines.
Groundlight’s Solution: Detecting Defects using Computer Vision

Groundlight’s computer vision technology works with operations using industrial robots and those without. A "plug and play" AI appliance called the Groundlight Hub plugs into your existing network and connects to your existing cameras. The cameras capture images of the products, and if Groundlight detects that a part does not pass quality control, it notifies the operator in real-time.
Groundlight Works With Your Existing Cameras
There simply needs to be a camera that captures images of the product, and Groundlight analyzes those images to determine if the part passes quality control. Cameras must be RTSP or ONVIF compatible.
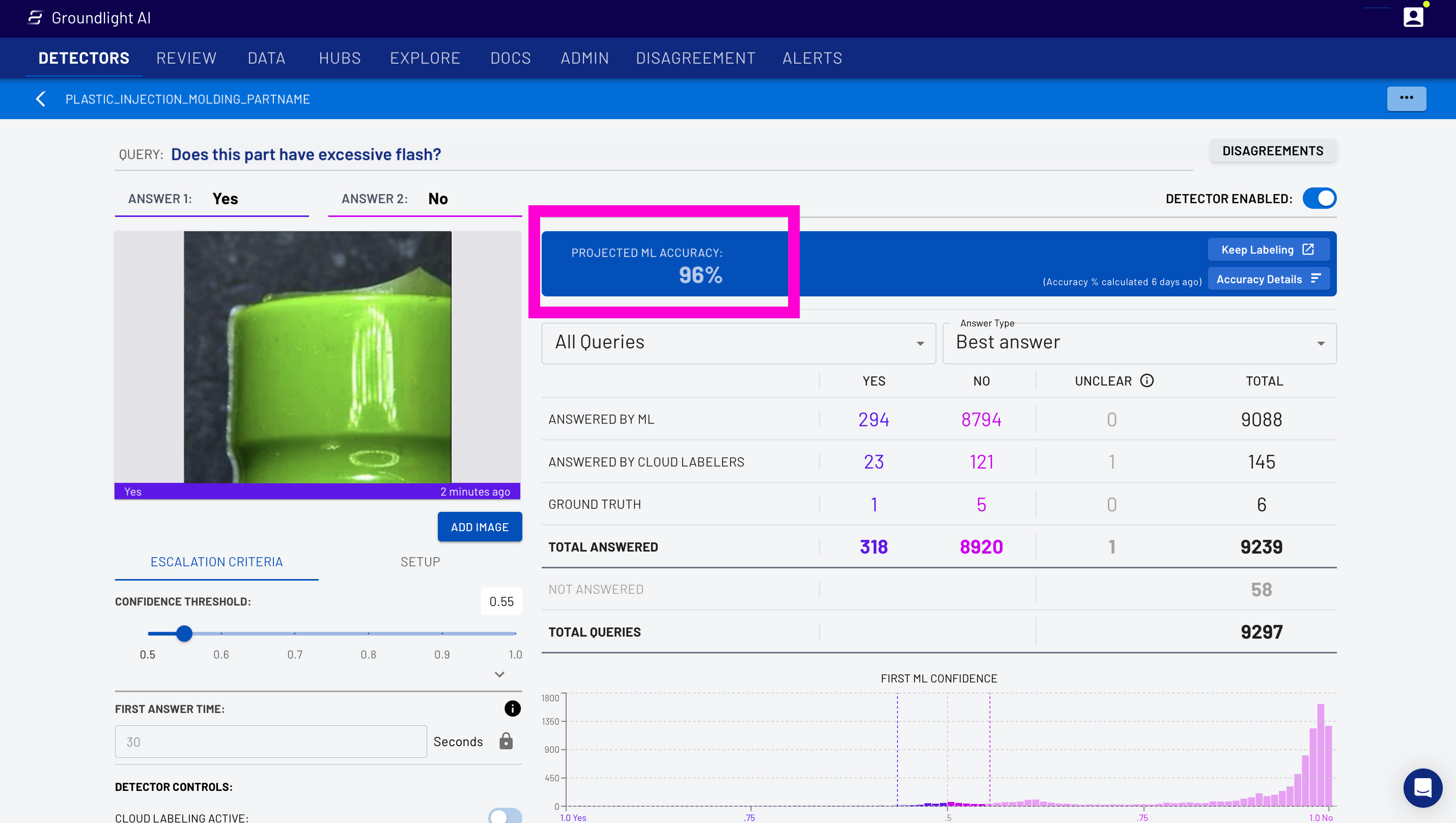
Key Quality Checks
The operator begins by defining what Groundlight's technology should look for (what "pass" and "fail" mean). This involves providing Groundlight with example images of acceptable parts and those with defects. These defects could include issues like flash, short shots, missing inserts, or surface irregularities. The system then uses its models to analyze new images in real time, determining whether a part meets quality standards.
In the event of a defect, Groundlight sends fully customizable notifications via text message or email, ensuring the right people are informed immediately. For example, an operator might receive a text stating “Defect detected. Batch # xxx-xxx part xxx-xxx at 10:30 AM”
With its intuitive setup, Groundlight starts working within minutes, delivering actionable results and enabling manufacturers to maintain high product quality while reducing downtime and operational inefficiencies. The system’s adaptability ensures it can be deployed across diverse manufacturing environments, making it a powerful solution for improving quality control at scale.
Key Features of Groundlight’s Defect Detection Solution:
- Real-Time Monitoring and Alerts: Provides immediate notifications of detected defects, enabling faster responses and minimizing downtime.
- Adaptable to Various Defects: Configurable to identify a wide range of defect types, from flash to surface irregularities, across diverse applications.
- Scalable Across Lines: Easily deployable across multiple production lines, ensuring consistent and efficient defect detection.
- Seamless Integrations: Compatible with existing workflows and production systems, including industrial robots like Universal Robots.
- Quick Setup: Design for rapid deployment, allowing the system to be operational in hours with minimal disruption.
- Continuous Learning: Human-guided AI improves accuracy over time, adapting to new production requirements and defect types.
- Inspection Reports: Generates comprehensive reports on defect detection, providing valuable data for quality assurance and process.
Impact
Implementing Groundlight’s defect detection solution offers significant benefits across multiple areas of manufacturing operations:
- Enhanced Product Quality: By identifying defects in real-time, the system ensures that only high-quality parts move forward in the production process. This minimizes the risk of defective products reaching customers, improving brand reputation and customer satisfaction.
- Cost Savings: Early defect detection reduces material waste, rework, and labor costs associated with manual inspections or fixing issues later in the process. Manufacturers can also avoid penalties or warranty claims caused by defective products.
- Improved Operational Efficiency: Automation reduces reliance on time-intensive manual inspections, allowing production lines to operate at higher speeds without compromising quality. Real-time alerts and streamlined workflows further reduce downtime and improve throughput.
- Scalability Across Production Lines: Groundlight’s solution is easily deployable across multiple lines and locations, adapting to varying production volumes and defect types. This scalability ensures consistent performance and quality control as manufacturing demands grow.
How Do I Get Started?
If you are a developer or have developers in-house, here’s how you can build this solution for yourself
SEE DOCUMENTATIONIf you’d like to customize this solution for your business but need assistance to get started, book a call with Groundlight and we’d be happy to help
Schedule a call